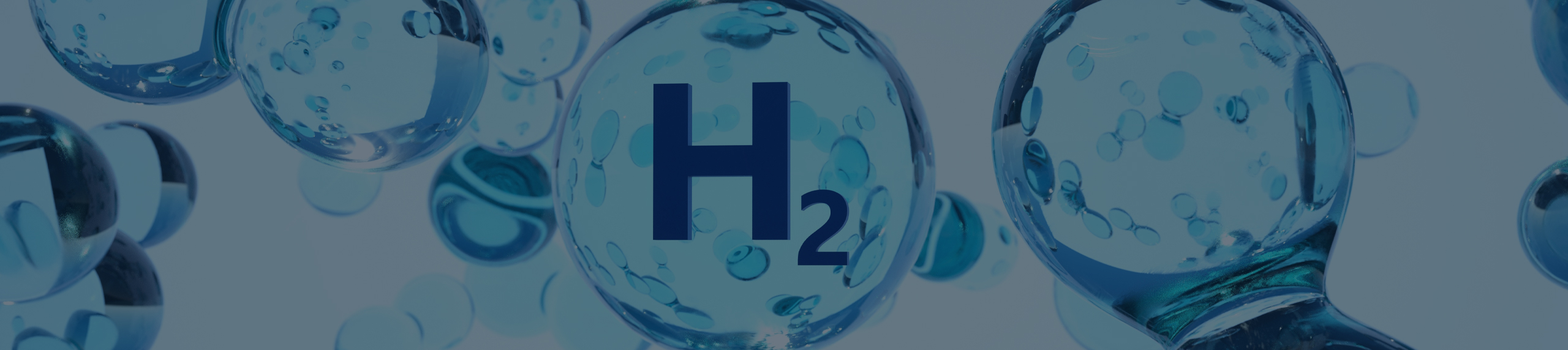
clean-tech-banner
Diffusion Alloys recognises the need for an industrial revolution to drive down carbon emissions and protect the planet for future generations.
The company incorporated this overriding objective into the heart of its business vision for clean, profitable growth which has, for a number of years, led the commercial direction of the company and driven its research and development program.
Diffusion Alloys has been at the forefront of the development and application of diffusion coatings to solve degradation issues in low carbon and clean technologies and our coatings provide demonstrable protection and life extension to large scale hydrogen generation units, solid oxide fuel cells systems, solid oxide electrolysers (SOE), energy storage, next generation nuclear and concentrated solar power (CSP).
Our diffusion coatings are designed to prevent a range of degradation issues, including metal dusting, oxidation, hydrogen permeation and chromium evaporation.
We understand that the development of clean technologies requires a collaborative and exploratory relationship to produce the best outcome technically and commercially for our customer.
Our experienced technical team work hand in hand with our clean technology customers to ensure a smooth path through from concept to demonstration to developed coating system.
With our significant experience in the requirements for the turbo-machinery industry, we have the quality mechanisms, processes and knowledge in place to deliver reliable and repeatable coatings.
The Company continues to invest in research and development which aligns with the Group goal of clean, profitable growth. Diffusion Alloys now has an exciting pipeline of R&D in place that fully supports decarbonisation objectives.
Hydrogen generation
Development of the hydrogen economy – ‘blue hydrogen’
Diffusion Alloys has extensive experience in the application of our aluminising to protect long tubes and other components from metal dusting that are used in steam reformer units to generate hydrogen. Our references with the major global technology licensees go back over 20 years.
Momentum politically and economically has continued to build around the use of ‘blue’ hydrogen and Diffusion Alloys has recognised and responded to customer’s requirements for larger units with the investment in its unrivalled 21m length furnace in Middlesbrough, UK, capable of aluminising tubes up to 18m (59ft) in length.
Diffusion Alloys has invested heavily in developing an understanding of customer requirements and recognises the criticality of the quality of an aluminide diffusion coating to the performance and lifetime capability of high efficiency steam reformer technology.
Development of the hydrogen economy – ‘green hydrogen’
Diffusion Alloys has been at the forefront of coating solutions for Solid Oxide Electrolyser components, to protect against corrosion. Our Technical colleagues work closely with our customers to deliver the required protection.
Mindful of the need for cost competitive green hydrogen production in the future we are seeking ways to support the supply chain for the decades to come.
Solid oxide fuel cells
An aluminium oxide scale prevents chromium in the base alloy from leaching out and poisoning a fuel cell stack and so can be critical to the lifetime performance of a solid oxide fuel cell. Diffusion Alloys has been working together with customers in this field for over ten years and we are proud to be part of its commercial success. Our staff have built up an enviable expertise in coating development and process control for complex geometries, small heat exchanger units and tight tolerances.
Nuclear
Liquid lead or lead-bismuth eutectic (LBE) is increasingly being considered over liquid sodium as the primary coolant for fast reactor systems as it allows for a compact format reactor due to the lower neutron absorption and relatively low melting points. Research shows that aluminide coatings have been proven to provide excellent corrosion resistance against liquid lead within the typical operating temperatures.
Energy storage
Our custom designed diffusion coatings are also being applied to various energy storage technologies (batteries and others) to prevent against hydrogen permeation, chromium evaporation and other corrosion mechanisms.
Concentrated Solar Power
Solar power plants widely use molten salt and best in class Solar Salt as the thermal energy storage mixture. The higher operating temperature however promotes faster corrosion of the tubes and tanks. Aluminide coatings, which permit the formation of a protective oxide layer have been demonstrated as highly effective against molten salt corrosion.
Research and development
Diffusion Alloys has R&D programs in place which will provide new coating technologies for our customers which are focused around improving our environmental footprint and/or enhancing the performance of coating and therefore extending life. These projects are our future will be offered commercially in due course.
We are at the forefront of applications for clean energy and the hydrogen industry.
Large-scale hydrogen generation
Hydrogen electrolysers (SOE)
Fuel cells (SOFC)
Energy storage
Nuclear
Other specialist life extension
With over 60 years of industry experience, we're a global specialist in the application of a range of protective coatings against metal degradation.
We have been supplying diffusion coating services for over 60 years. In 1955 the Company became the first company world-wide to launch chromising as a commercial industrial diffusion coating.
We have decades of experience in coatings for the industrial gas turbine market and the oil, gas and process industries and have developed a leading position in diffusion coating for clean technology applications.
We consider the Health & Safety of its employees, customers, visitors and the general public to be of prime importance. We take an ethical approach to our environmental responsibility & waste management.
We pride ourselves on consistently scoring as best coating supplier for quality with a number of our major and long term customers which is testimony to our quality management system.