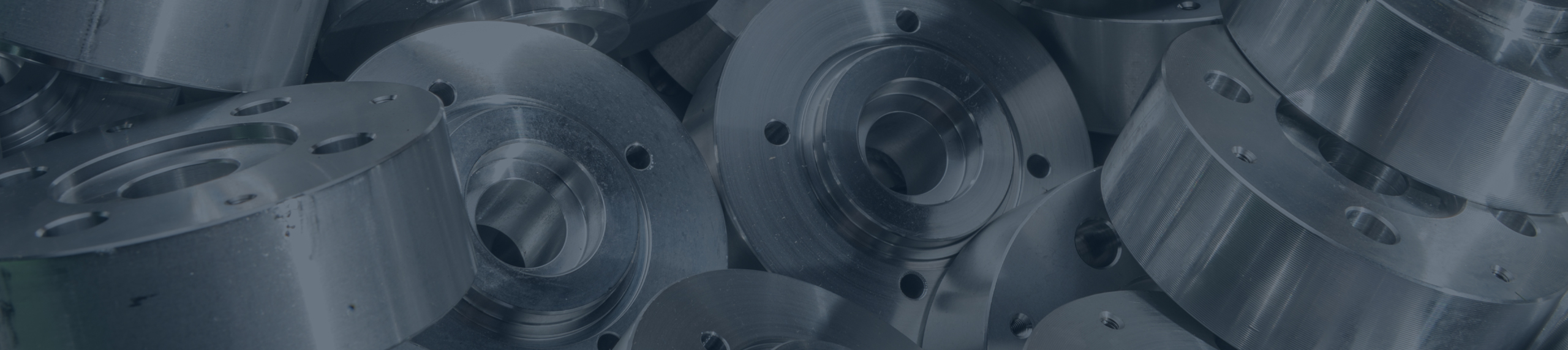
Chromizing
Chromising is a surface treatment carried out at elevated temperatures in which an alloy is formed by the inward diffusion of chromium into the base metal.
Diffusion Alloys was the first company world-wide to launch (in the 1950s) chromising as a commercial industrial diffusion coating process.
Properties and Uses of Chromising (Chromizing)
Chromising can protect components from corrosion, wear, abrasion and oxidation. Chromide diffusion coatings were originally developed by Diffusion Alloys for hot section industrial gas turbine blades and vanes to protect them against high temperature oxidation and hot corrosion. Over the years, chromised component applications have widened considerably and we now coat for a wide range of industries, including oil & gas, process, steel, textile and renewables.
Our chromide coatings do not contain hexavalent chromium.
Steels with carbon content greater than 0.3% can form a hard dense diffused chromium carbide surface layer which has high hardness and excellent wear resistance. Typical materials that are suitable for chromising / chromizing include:
Low carbon steels:
Oxidation resistance to 650℃; corrosion resistance similar to ferritic stainless steel
Medium carbon steels:
Light wear and corrosion resistance
High carbon steel:
Wear resistance and corrosion resistance
Stainless steels:
Wear resistance and corrosion resistance
Nickel & Cobalt base super alloys:
Corrosion and erosion resistance
Diffusion Alloys’ Chromising Facilities and Processes
For the application of our chromide diffusion coatings, we operate air furnaces (glass sealed box method) and various sizes of furnaces operating under protective atmospheres. In our largest furnace, we can chromise large components up to 18 metres (59 ft) in length.
We apply our chromide coatings by pack cementation.
Pack Cementation
Pack cementation is our most widely used diffusion coating process and is performed in either a glass seal box in-air furnace or in a reducing/inert gas atmosphere retort. The chosen components are embedded in a powder mixture as the ‘pack’ or ‘compound’ which consists of:
- A source metal: Cr (may be moderated)
- An activator (e.g. Halide)
- An inert diluent (e.g. Al₂O₃; prevents pack powder particles sintering together)
At the required coating temperature, the activator reacts with the source metal to form a gaseous halide compound, which is transferred to the substrate surface. As this gas decomposes, the halogen activator is released and the coating element is deposited at the substrate surface, leaving the activator to return to the pack and react with the source metal again.
Several methods are available to mask areas on components which must not be coated during the process.
Summary
In concert with an extensive menu of diffusion coating compounds we are able to offer tailor-made solutions to customer diffusion coating requirements. To minimise costs, all but a very few of these compounds can be regenerated for continual re-use. Stringent quality control procedures are in place to guarantee compound properties, with each batch individually checked prior to release. Similarly, representative and strategically located test pieces accompany every diffusion coating run to facilitate in-process control and certification.
Chromising can also be referred to as Chromizing.
We are at the forefront of applications for clean energy and the hydrogen industry.
Large-scale hydrogen generation
Hydrogen electrolysers (SOE)
Fuel cells (SOFC)
Energy storage
Nuclear
Other specialist life extension
With over 60 years of industry experience, we're a global specialist in the application of a range of protective coatings against metal degradation.
We have been supplying diffusion coating services for over 60 years. In 1955 the Company became the first company world-wide to launch chromising as a commercial industrial diffusion coating.
We have decades of experience in coatings for the industrial gas turbine market and the oil, gas and process industries and have developed a leading position in diffusion coating for clean technology applications.
We consider the Health & Safety of its employees, customers, visitors and the general public to be of prime importance. We take an ethical approach to our environmental responsibility & waste management.
We pride ourselves on consistently scoring as best coating supplier for quality with a number of our major and long term customers which is testimony to our quality management system.