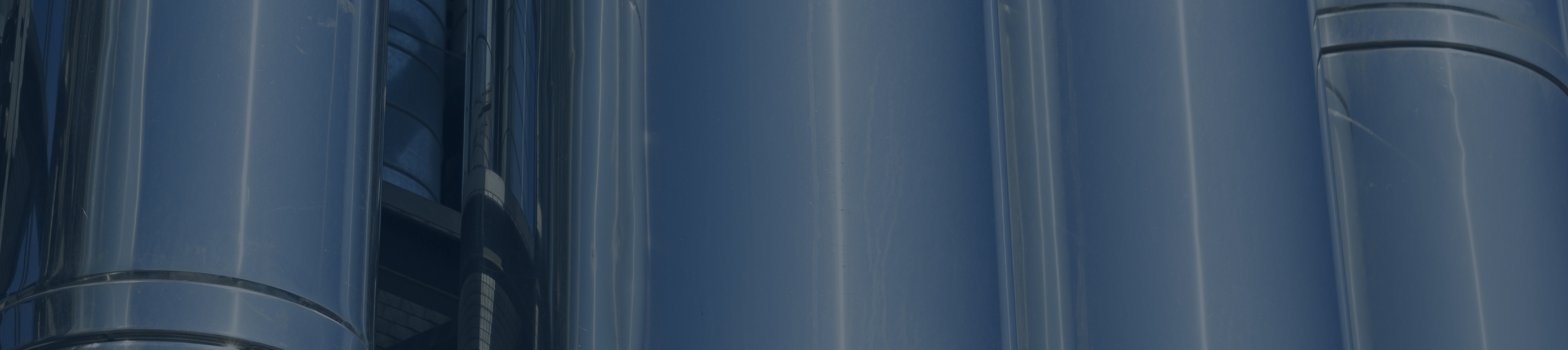
Aluminizing
Aluminising, sometimes referred to as Alonizing and Calorizing, is a high temperature chemical process whereby aluminium diffuses into the surface of the base metal to form a metallurgical aluminide surface layer.
Diffusion Alloys is a global leader in the provision of aluminide diffusion coatings, offering the widest range of applications for aluminising of any company in the market.
Properties and Uses of Aluminising
Aluminide diffusion coatings offer protection in medium and high temperature operating environments against:
- Hot Corrosion
- Metal Dusting
- Oxidation
- Carburisation
- Sulfidation
- Hydrogen permeation
- Chromium leach
This protection is conferred by the aluminium oxide that forms at the aluminide coating surface in service. This oxide constitutes an extremely effective barrier. The aluminide coating essentially acts as an aluminium reservoir to maintain and support the aluminium oxide. Materials suitable for aluminising include mild steel, low alloy steels, cast/wrought stainless steels, nickel-base alloys and nickel-iron alloys.
Areas of application for aluminide coatings are still evolving. For years, aluminide diffusion coatings have been widely applied applied to turbo-machinery components to protect the external and internal cooling channel surfaces of gas turbine blades and vanes. Aluminide coatings also find common application in process industries such as chemical, petrochemical and iron and steel. More latterly, applications in clean energy technologies have arisen as emerging technologies encounter metal degradation complexities within high temperature systems.
Diffusion Alloys’ Aluminising Facility and Processes
For the application of our range of aluminide diffusion coatings we can cater for the large and small. We have a comprehensive range of air furnaces (glass sealed box method) and furnaces that operate under protective atmospheres.
We have been aluminising long tubes/pipes and large parts in Middlesbrough since 1985 and have the largest aluminising furnace (at 21m length) of any supplier in the world, enabling us to coat tubes of up to 18m in length.
Aluminising of components is carried out using one of four processes.
Pack Cementation
Our most widely used process is performed in either a glass seal box in an air furnace or in a reducing/inert gas atmosphere retort.
The chosen components are embedded in a proprietary powder mixture referred to as the ‘pack’ or ‘compound’ which consists of:
- A source metal: Al (may be moderated)
- An activator (e.g. Halide)
- An inert diluent (e.g. Al₂O₃; prevents pack powder particles sintering together)
At the required coating temperature, the activator reacts with the source metal to form a gaseous halide compound, which is transferred to the substrate surface. As this gas decomposes, the halogen activator is released and the coating element is deposited at the substrate surface, leaving the activator to return to the pack and react with the source metal again.
Coating thickness is controlled by temperature and time at temperature. For example, components to be aluminide diffusion coated can be packed in aluminising compound within steel retorts, heated slowly to a temperature within the range 900 – 1050°C, held at temperature for 24 – 48 hours then slow cooled to ambient temperature.
Components may be simultaneously aluminised both internally (by filling them with compound) and externally, or external or internal only aluminide coatings may be applied.
Above-Pack Vapour
Very similar to the pack cementation method; however, components to be coated are placed above and hence out of contact with the pack. Whether this method is the most appropriate depends on the component geometry as the increased path length for halide transport generally involves reduced deposition rates.
Slurry
This method allows coating of specific areas and local diffusion coating repair. Slurries consist of an organic binder mixed in equal parts with water, to which variants of reactive pack mixture are added.
Depending on their composition our slurries can be applied either by painting or pasting. Areas not to be coated are masked to ensure no slurry is applied to these areas.
Summary
In concert with an extensive menu of diffusion coating compounds we are able to offer tailor made solutions to any customer’s diffusion coating requirements.
To minimise costs, all but a very few of these compounds can be regenerated for continual re-use.
Stringent quality control procedures are in place to guarantee compound properties, with each batch individually checked prior to release.
Similarly, representative and strategically located test pieces accompany every diffusion coating run to facilitate in-process control and certification.
Aluminising can also be referred to as Aluminizing, AlonizingTM and Calorizing.
We are at the forefront of applications for clean energy and the hydrogen industry.
Large-scale hydrogen generation
Hydrogen electrolysers (SOE)
Fuel cells (SOFC)
Energy storage
Nuclear
Other specialist life extension
With over 60 years of industry experience, we're a global specialist in the application of a range of protective coatings against metal degradation.
We have been supplying diffusion coating services for over 60 years. In 1955 the Company became the first company world-wide to launch chromising as a commercial industrial diffusion coating.
We have decades of experience in coatings for the industrial gas turbine market and the oil, gas and process industries and have developed a leading position in diffusion coating for clean technology applications.
We consider the Health & Safety of its employees, customers, visitors and the general public to be of prime importance. We take an ethical approach to our environmental responsibility & waste management.
We pride ourselves on consistently scoring as best coating supplier for quality with a number of our major and long term customers which is testimony to our quality management system.