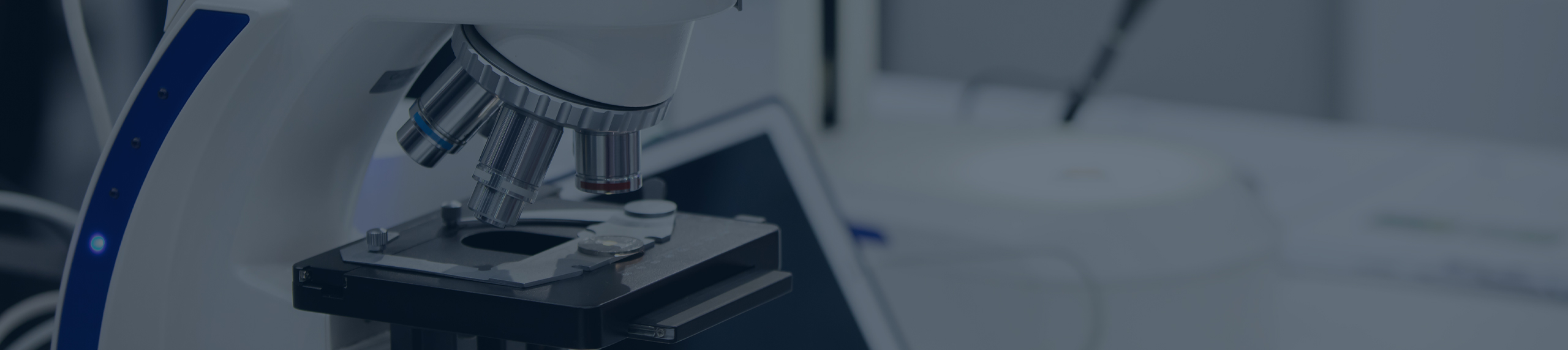
Lab Services
The metallurgical laboratory sits within the Technical Department and is the cornerstone of the quality control and analysis of both coated products and raw materials for the company.
It is also instrumental in failure investigations.
With a suite of metallurgical and chemical analysis techniques the laboratory is well placed to demonstrate conformance of coatings with a wide range of customer and ASTM specifications.
The laboratory is able to offer its services to aid with:
- Sample preparation.
- Coating characterisation.
- Failure investigations.
- Chemical analysis.
- Metallurgical analysis.
Sample preparation
Every sample analysed by the laboratory requires preparation prior to analysis being carried out in order to ensure accurate microstructures are revealed. The key steps in this preparation are sectioning, mounting, grinding, polishing and etching.
The lab is equipped with various cutting wheels and discs to enable accurate sectioning of the region of interest from a sample.
Following sectioning parts are mounted into a thermally set epoxy resin. The mounting process minimises the amount of damage likely to be caused to the specimen and is important for edge retention of the sample.
The grinding operation removes any surface layers of material that may have been damaged by the cutting process. The mounted specimens are ground using a series of silicon carbide papers that are successively finer.
The polishing operation uses a colloidal silica and removes any scratches from the grinding step leaving a smooth surface with a characteristic mirror finish.
Metallic samples are then typically etched to reveal microstructures not visible on the as polished samples. The laboratory has a range of etchants to enable analysis of a wide range of metal substrates.
Please contact us today to discuss your sample preparation requirements at enquiries@diffusion-alloys.com.
Coating Characterisation
The core function of the laboratory is to provide extensive analysis of our coatings to determine conformance to a range of specifications.
The laboratory is equipped with optical microscopes and an Scanning Electron Microscope (SEM) fitted with an energy dispersive x-ray spectrometer (EDS).
Optical microscopy enables a coating (or metal substrate) to be evaluated in terms of its:
- Uniformity.
- Thickness.
- Presence of defects.
The optical microscopes enable evaluation of a surface at 50, 100, 200 and 500x magnification.
Each microscope is connected to image capturing software so images of the artifact being analysed can be captured at each magnification.
For coatings on silicon carbide and tungsten carbide substrates the laboratory also has a ball cratering device for evaluating coating thicknesses.
The SEM-EDX is used to determine the chemical composition of coatings and enables the monitoring of key elements through the depth of the coating. As a semi quantitative technique it can also be used to provide approximate stoichiometries and compositions of the coating/ material being analysed.
The SEM-EDX enables surfaces to be viewed at up to several thousand times magnification enabling evaluation of much smaller regions of a sample than with optical microscopy.
Please contact us today to discuss your coating characterisation requirements at enquiries@diffusion-alloys.com.
Failure investigations
Determining the root cause of failures is a key aspect of the laboratory work.
This typically involves evaluation and analysis by optical microscopy and Scanning Electron Microscope (SEM) fitted with an energy dispersive x-ray spectrometer (EDS). For more detail on these two techniques please see our coating characterisation capabilities.
The analysis can be performed on metallic samples, coatings or even on powders. This enables the fault and individual materials in the area of a failure to be identified, evaluated and characterised. Examples of different forms of defects that can be analysed include indents to a base material, weld damage, or surface deposits/debris.
Examples of the failure analysis that can be offered by the laboratory include:
- Cross sectional analysis of defects.
- Determination of chemical composition of defects.
- Use of positive material identification in the form of a portable x-ray fluorescence (XRF) spectrometer.
- Hardness testing with Vickers (macro and micro) and Rockwell testers.
If you need support with failure analysis please contact us today to discuss how our laboratory could help at enquiries@diffusion-alloys.com.
Chemical analysis
The laboratory regularly performs chemical analysis on samples in either metallic or powder form. The key analytical techniques for chemical analysis in our laboratory are Scanning Electron Microscopy (SEM) with energy dispersive x-ray spectrometry (EDS), our portable x-ray fluorescence (XRF) spectrometer and our atomic absorption spectrometer (AAS).
Bothe SEM/EDS and XRF offer chemical compositional analysis. The XRF offers the advantage of being able to perform analysis on any size component in solid or powder form. The SEM/EDS is better suited for analysis of localised regions of a component or samples that can be sectioned.
The AAS is capable of determining the concentration of acid soluble aluminium, chromium or iron in powders.
If you need support in chemical analysis please contact us today to discuss your requirements and how we can help at enquiries@diffusion-alloys.com.
Metallurgical analysis
The metallurgical analysis complements our chemical analysis offering further characterisation in the form of material properties analysis primarily in the form of hardness testing.
There are three hardness testers available in the laboratory a Vickers macro hardness tester, a Vickers micro hardness tester and a Rockwell Hardness tester.
If you have a specific hardness testing requirement please contact us today to discuss how our laboratory could help at enquiries@diffusion-alloys.com.
We are at the forefront of applications for clean energy and the hydrogen industry.
Large-scale hydrogen generation
Hydrogen electrolysers (SOE)
Fuel cells (SOFC)
Energy storage
Nuclear
Other specialist life extension
With over 60 years of industry experience, we're a global specialist in the application of a range of protective coatings against metal degradation.
We have been supplying diffusion coating services for over 60 years. In 1955 the Company became the first company world-wide to launch chromising as a commercial industrial diffusion coating.
We have decades of experience in coatings for the industrial gas turbine market and the oil, gas and process industries and have developed a leading position in diffusion coating for clean technology applications.
We consider the Health & Safety of its employees, customers, visitors and the general public to be of prime importance. We take an ethical approach to our environmental responsibility & waste management.
We pride ourselves on consistently scoring as best coating supplier for quality with a number of our major and long term customers which is testimony to our quality management system.