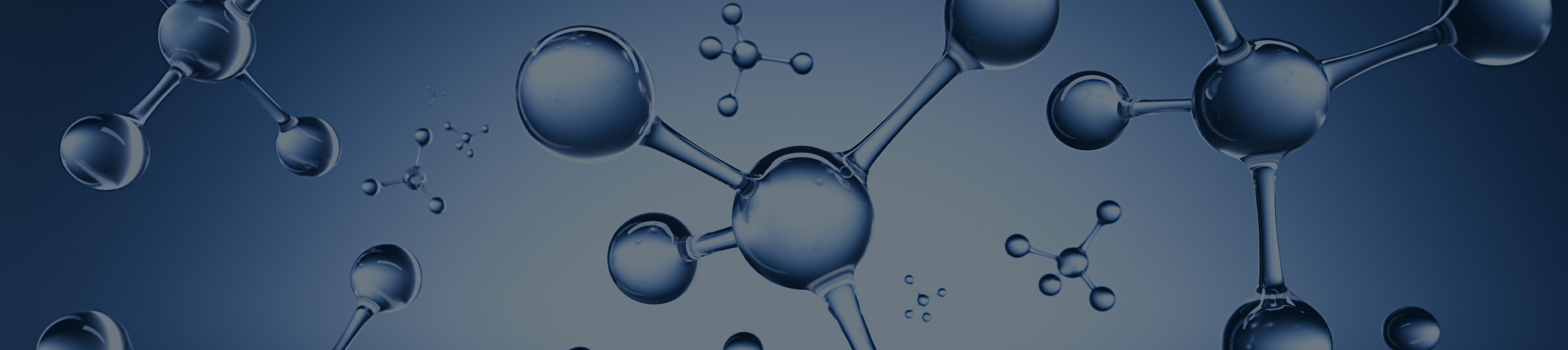
Unlocking the Potential of Diffusion Coatings: Benefits, Applications, and Techniques
In the realm of surface engineering, diffusion coatings emerge as a versatile and impactful method for fortifying the properties of materials.
From bolstering wear resistance to augmenting corrosion protection, diffusion coatings offer a plethora of advantages across diverse industries. This blog post aims to unravel the realm of diffusion coatings, elucidating key aspects to furnish a comprehensive understanding of their significance, applications, and methodologies.
What is Diffusion Coating?
Diffusion coating denotes a surface treatment process wherein one or more elements permeate the surface of a substrate material through diffusion at elevated temperatures. This transformative process engenders the formation of a thin, adherent layer imbued with modified chemical and mechanical properties vis-à-vis the substrate material.
Types of Diffusion Coatings:
Diverse types of diffusion coatings are tailored to meet specific performance requisites. Noteworthy variants encompass:
• Aluminising: Facilitates the diffusion of aluminium into the substrate material to bolster oxidation resistance and high-temperature performance.
• Chromising: Harnesses chromium diffusion to enrich corrosion resistance and wear properties.
• Nitriding: Infuses nitrogen into the surface to enhance hardness, wear resistance, and fatigue life.
• Boriding: Fosters boron diffusion to amplify hardness, wear resistance, and corrosion resistance.
• Carburising: Introduces carbon into the surface to amplify hardness and wear resistance.
Applications of Diffusion Coatings:
Diffusion coatings find extensive applications across multifarious industries, including:
• Aerospace: Elevates the performance of turbine blades, engine components, and aerospace structures by fortifying wear and corrosion resistance.
• Automotive: Applied to engine components, gears, and transmission parts to augment durability and reliability.
• Oil & Gas: Employed in downhole tools, valves, and pipelines to mitigate wear and corrosion in arduous operating environs.
• Tooling: Enhances the longevity and performance of cutting tools, moulds, and dies.
• Energy: Utilised in power generation equipment, such as turbine blades and steam valves, to withstand high-temperature and corrosive conditions.
Benefits of Diffusion Coatings:
The manifold benefits of diffusion coatings encompass:
• Enhanced wear resistance: Augmented surface hardness and diminished friction contribute to elongated component lifespan.
• Amplified corrosion resistance: Safeguards against chemical and environmental degradation extend the service life of coated components.
• Augmented high-temperature performance: Resistance to oxidation and thermal cycling ensures reliability in demanding applications.
• Tailored properties: Customisable coating compositions and thickness afford precise control over material properties.
• Cost-effectiveness: In comparison to alternative surface treatment methodologies, diffusion coatings proffer a cost-efficient solution for improving component performance and longevity.
Diffusion Coating Techniques:
Various techniques, including pack cementation, chemical vapour deposition (CVD), physical vapour deposition (PVD), and plasma spraying, are instrumental in applying diffusion coatings. Each technique confers distinct advantages and is chosen based on factors such as substrate material, coating thickness, and application requisites.
Conclusion:
Diffusion coatings serve as a pivotal asset in enhancing the performance and durability of materials across a plethora of industries. By comprehending the fundamentals of diffusion coating, alongside its applications, benefits, and techniques, manufacturers and engineers can harness this technology to optimise component performance, curtail maintenance costs, and elongate the service life of critical equipment. Whether in aerospace, automotive, or energy sectors, the versatility and efficacy of diffusion coatings continue to propel innovation and progress in surface engineering.