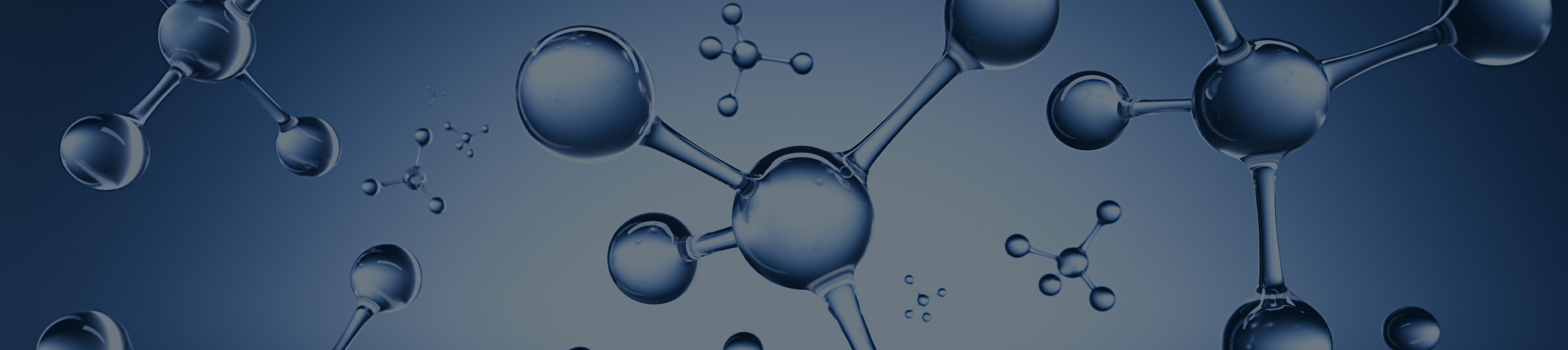
What is Boronising?
Explore the world of boronising, a surface-hardening technique with a rich history and diverse applications.
Originating in the early 20th century and gaining prominence during World War II, boronising has revolutionised metal strengthening. This process involves infusing boron into metal surfaces at high temperatures, resulting in remarkable enhancements in hardness, wear, and corrosion resistance. From pack to gas and plasma boronising, each method offers unique advantages. With applications spanning automotive, aerospace, and tooling industries, boronising stands as a cornerstone of modern manufacturing.
Join us as we delve into the top 20 fascinating facts about this indispensable process.
1. Process Origins: Boronising dates back to the early 20th century and gained industrial significance during World War II for hardening steel parts.
2. Materials: Boronising is primarily used on ferrous metals such as steel, iron, and certain alloys.
3. Process: Boronising involves heating the metal part in the presence of a boron-containing material at high temperatures, typically between 800°C to 1050°C (1472°F to 1922°F).
4. Diffusion: Boron atoms diffuse into the surface of the metal, forming borides that significantly increase surface hardness.
5. Types of Boronising: There are several methods of boronising, including pack boronising, gas boronising, and plasma boronising, each with its advantages and applications.
6. Pack Boronising: In pack boronising, the metal part is packed in a powder mixture containing boronising agents, such as boron carbide, borax, and amorphous boron.
7. Gas Boronising: Gas boronising involves exposing the metal part to a boron-containing gas, such as boron trifluoride or diborane, at elevated temperatures.
8. Plasma Boronising: Plasma boronising utilises a plasma containing boron compounds to bombard the metal surface, facilitating boron diffusion.
9. Hardness Improvement: Boronising significantly increases surface hardness, typically achieving hardness values between 1000 to 2000 HV (Vickers hardness), depending on the process parameters and materials.
10. Wear Resistance: Boronised surfaces exhibit excellent wear resistance, making them suitable for applications subjected to abrasive wear, erosion, and sliding.
11. Corrosion Resistance: Boronising enhances the corrosion resistance of metal surfaces, particularly in harsh environments where corrosion is a concern.
12. Uniform Coating: Boronising produces a uniform coating thickness, ensuring consistent hardness and performance across the treated surface.
13. Depth of Penetration: The depth of boron penetration can vary depending on process parameters but typically ranges from 25 to 2000 micrometres.
14. Applications: Boronising finds applications in various industries, including automotive, aerospace, oil and gas, tooling, and manufacturing of wear-resistant components.
15. Tooling: Boronising is commonly used for hardening cutting tools, dies, gears, and other components subjected to high wear and abrasion.
16. Automotive Industry: In the automotive industry, boronising is used to harden engine components, such as camshafts, crankshafts, and transmission gears, to improve durability and performance.
17. Heat Treatment Compatibility: Boronising can be combined with other heat treatment processes, such as quenching and tempering, to achieve desired material properties.
18. Environmental Impact: Boronising is generally considered an environmentally friendly process compared to some other surface-hardening methods, as it typically doesn’t involve hazardous chemicals or generate harmful by-products.
19. Cost Considerations: While boronising can increase the initial cost of manufacturing, the improved performance and extended service life of boronised components often result in long-term cost savings.
20. Research and Development: Ongoing research and development efforts continue to refine boronising processes, optimise parameters, and explore new applications, ensuring its continued relevance and effectiveness in modern industry.