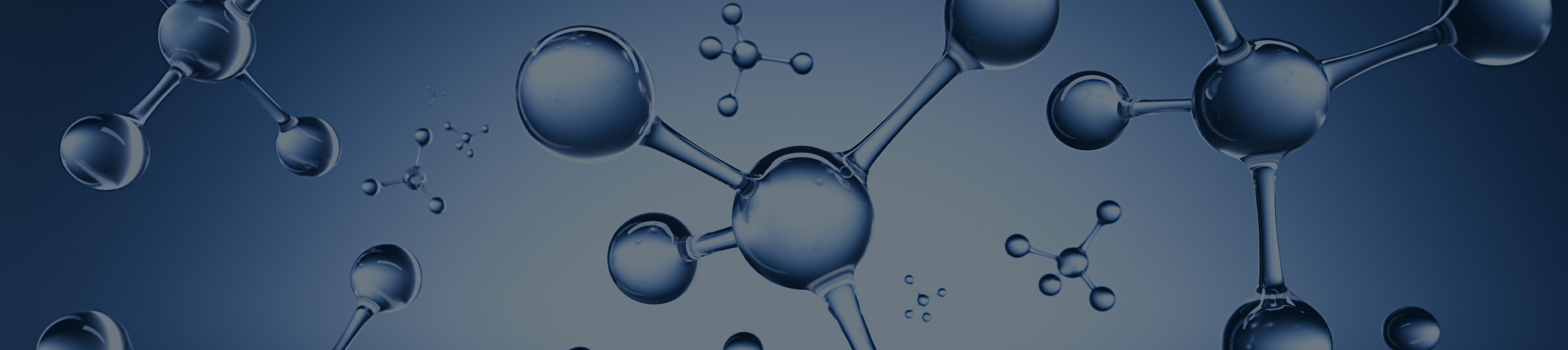
What is Aluminizing?
Aluminizing is a metallurgical process that involves the deposition of a layer of aluminum onto the surface of a substrate, typically metal. This technique is primarily employed to enhance the corrosion resistance, oxidation resistance, and overall durability of the substrate.
Aluminizing is widely used in various industries, including aerospace, automotive, and energy production, owing to its ability to extend the lifespan of components subjected to harsh environments.
Process of Aluminizing
The aluminizing process can be executed through several methods, with pack cementation, hot-dip aluminizing, and vapor phase aluminizing being the most common.
Pack Cementation: This method involves packing the substrate with a mixture of aluminum powder, an activator (like ammonium chloride or fluoride), and an inert filler (such as alumina). The packed substrate is then heated in a furnace to a temperature where aluminum can diffuse onto the surface of the substrate. This process forms a protective aluminide layer, which is usually an intermetallic compound of aluminum and the base metal.
Hot-Dip Aluminizing: In this method, the substrate is immersed in a bath of molten aluminum. The substrate, pre-cleaned to ensure good adhesion, is dipped into the molten aluminum at high temperatures. Upon withdrawal and cooling, a thick, protective aluminum coating forms on the surface. This method is often used for larger components and provides a robust coating.
Vapor Phase Aluminizing: This technique involves the use of aluminum halide gases to deposit aluminum onto the substrate. The substrate is exposed to aluminum chloride vapors at elevated temperatures, allowing aluminum to deposit and form a protective layer. This method is beneficial for coating complex shapes and internal surfaces.
Benefits of Aluminizing
Corrosion Resistance: The primary advantage of aluminizing is the significant improvement in corrosion resistance. The aluminum layer acts as a barrier, preventing corrosive elements such as oxygen and moisture from reaching the underlying metal. This makes aluminizing particularly useful for components exposed to harsh environmental conditions, like offshore structures and pipelines.
Oxidation Resistance: Aluminized surfaces exhibit excellent resistance to high-temperature oxidation. This is because aluminum forms a stable oxide layer (alumina) when exposed to high temperatures, protecting the substrate from further oxidation. This property is crucial for components in high-temperature environments, such as turbine blades and exhaust systems.
Durability and Wear Resistance: The aluminide layer enhances the surface hardness and wear resistance of the substrate. This is particularly beneficial for components subjected to mechanical wear and abrasion, extending their operational life.
Thermal Stability: Aluminized coatings maintain their protective properties even at elevated temperatures, making them suitable for use in thermal power plants and other high-heat applications.
Applications of Aluminizing
Aerospace: Components like turbine blades, exhaust ducts, and engine parts benefit from aluminizing due to improved high-temperature performance and oxidation resistance.
Automotive: Aluminizing is used for exhaust systems, heat shields, and other parts exposed to high temperatures and corrosive environments.
Energy Production: Boilers, heat exchangers, and piping systems in power plants are often aluminized to enhance their resistance to high-temperature oxidation and corrosion.
Aluminizing and the Services Offered by Diffusion Alloys
Diffusion Alloys is a company that specializes in surface engineering and protective coating technologies, including various diffusion coating processes. They offer services aimed at enhancing the performance and lifespan of components used in demanding environments. Specifically, Diffusion Alloys provides aluminizing services through different methods, such as pack cementation and vapor phase aluminizing.
Pack Cementation at Diffusion Alloys
This method involves coating components with a mixture of aluminum powder, activators, and inert fillers. The components are then heated in a controlled atmosphere, allowing aluminum to diffuse into the substrate and form a protective aluminide layer. This process is beneficial for enhancing the surface properties of components used in industries such as aerospace, power generation, and petrochemical processing.
Vapor Phase Aluminizing at Diffusion Alloys
Diffusion Alloys also employs vapor phase aluminizing, which uses aluminum halide gases to deposit aluminum onto the surface of components. This method is advantageous for coating complex shapes and internal surfaces, ensuring comprehensive protection. The resulting aluminide layer provides excellent oxidation and corrosion resistance, particularly in high-temperature applications.
Other Services by Diffusion Alloys
In addition to aluminizing, Diffusion Alloys offers a range of other diffusion coating services, including:
Chromizing: This process involves the diffusion of chromium into the surface of metal components, enhancing their hardness, wear resistance, and corrosion resistance. Chromizing is commonly used for components subjected to high wear and corrosive environments.
Siliconizing: Siliconizing involves the diffusion of silicon into the substrate, forming a protective silicide layer. This layer improves high-temperature oxidation resistance and can be used in applications such as turbine blades and heat exchangers.
Boriding (Boronizing): This process diffuses boron into the surface of metals, significantly increasing hardness and wear resistance. It is particularly useful for components that experience severe mechanical wear.
Applications of Diffusion Alloys’ Services
Diffusion Alloys’ coating services are applied across various industries, including:
Aerospace: Protection of turbine blades, exhaust systems, and other high-temperature components.
Automotive: Coating of exhaust systems, turbocharger components, and heat shields.
Power Generation: Protection of boilers, heat exchangers, and piping systems from high-temperature corrosion and oxidation.
Petrochemical: Coating of reactors, distillation columns, and other equipment exposed to corrosive chemicals.
In conclusion, aluminizing is a versatile and effective surface treatment process that significantly enhances the performance and longevity of metal components. Diffusion Alloys provides comprehensive aluminizing services, along with other advanced diffusion coating processes, ensuring that components receive the necessary protection to withstand harsh operating conditions. Their expertise in surface engineering makes them a valuable partner for industries seeking to improve the durability and resistance of their components.