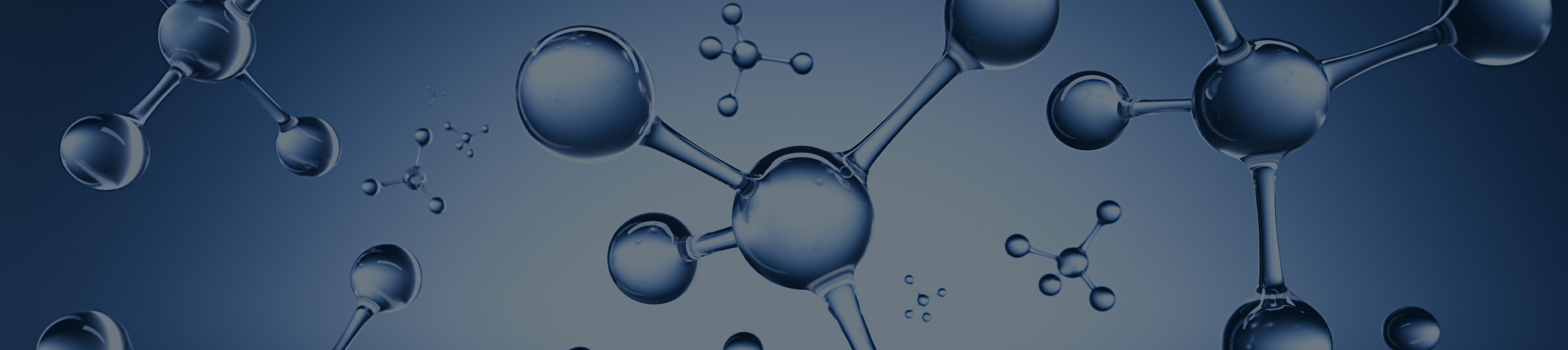
Top 10 Facts About Aluminizing
Historical Background: Aluminizing has been in use for several decades, initially developed for applications requiring high-temperature oxidation resistance. The process has evolved over time, integrating more advanced techniques and applications.
Variety of Methods: Aluminizing can be performed using various methods, including pack cementation, vapor phase aluminizing, slurry coating, and hot-dip aluminizing. Each method offers unique advantages and is suitable for different types of components and applications.
Wide Range of Substrates: Aluminizing is applicable to a variety of substrates, including steel, nickel, and cobalt-based alloys. This versatility makes it useful across many industries with different material requirements.
Formation of Protective Layers: During the aluminizing process, the aluminum diffuses into the substrate to form aluminide compounds. These compounds, such as iron aluminide (FeAl) or nickel aluminide (NiAl), are highly stable and offer excellent protection against oxidation and corrosion.
Temperature Resistance: Aluminized coatings can withstand extreme temperatures, often up to 1100°C (2012°F). This makes them ideal for high-temperature applications, such as gas turbines and furnace components.
Environmental Benefits: Aluminizing can extend the lifespan of components, reducing the need for frequent replacements and lowering overall material consumption. This contributes to more sustainable industrial practices.
Customizable Coatings: The thickness and composition of aluminized coatings can be tailored to meet specific performance requirements. This customization allows for optimal protection and functionality for various applications.
Improved Surface Properties: In addition to corrosion and oxidation resistance, aluminized surfaces often exhibit enhanced mechanical properties, such as increased hardness and wear resistance. This improves the durability and performance of treated components.
Compatibility with Other Coatings: Aluminized layers can serve as a base for additional coatings, such as ceramic or thermal barrier coatings. This multi-layer approach further enhances the protection and performance of the underlying substrate.
Economic Advantages: Although the initial cost of aluminizing can be higher than some other surface treatments, the extended lifespan and improved performance of aluminized components often result in significant long-term cost savings. Reduced maintenance and replacement costs contribute to overall economic benefits.
Why Aluminizing is Beneficial
Aluminizing is highly beneficial because it significantly enhances the performance and longevity of metal components. By depositing a layer of aluminum onto the surface, aluminizing provides exceptional corrosion and oxidation resistance, crucial for components exposed to harsh environmental conditions and high temperatures. This protective layer prevents the underlying metal from degrading, thus extending the lifespan of parts used in critical applications like aerospace turbines, automotive exhaust systems, and power plant boilers. Additionally, aluminized surfaces exhibit increased hardness and wear resistance, which improves the durability and mechanical performance of the components. This leads to reduced maintenance costs and downtime, offering long-term economic advantages. Furthermore, the process is versatile and can be tailored to various substrates and requirements, making it a valuable solution across multiple industries.