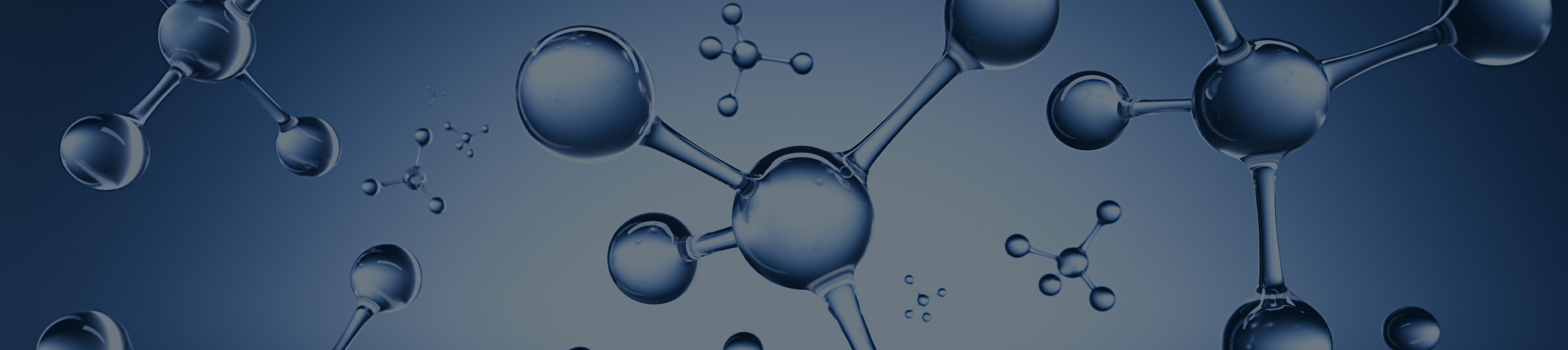
Boronizing Process Overview
Boronizing, also known as boriding, is a thermochemical surface-hardening process in which boron atoms are diffused into the surface of a workpiece to form complex borides, such as FeB and FeB2, with the base metal.
This true diffusion process ensures no mechanical interface between the complex borides and the substrate. The resulting case layer has a hard, slippery surface capable of performing at higher temperatures than most surface treatments. Nearly any ferrous material can be boronized, as well as many nickel, titanium, and cobalt alloys. However, the higher the alloy element content, the slower the diffusion rate.
Benefits of Boronizing
Boronizing is used to enhance the life and performance of metal components.
The process:
• Strengthens resistance to corrosion
• Strengthens resistance to acid
• Strengthens resistance to abrasive wear
• Decreases coefficient of friction
• Increases surface hardness
Examples of applications include pumps, valves, and impellers. Its properties of extreme abrasion and erosion resistance make it suitable for the oil, mining, and agricultural industries.
Boronizing Process Details
Boronizing is a metallurgical surface preparation method in which metal is heated in a boron-rich environment to increase wear resistance. This boron diffusion process creates a hard, wear-resistant case beneath the surface of various ferrous and non-ferrous materials. The process uses specially formulated boron-yielding materials heated to temperatures between 1300 and 1830°F (704 to 999°C).
During boronizing, boron atoms diffuse into the metal surface, forming metal borides. These surface borides may be in the form of either a single-phase or a double-phase boride layer. In ferrous materials, the boride layers achieve a hardness of between 1500HV and 2300HV. Boronized metal parts are extremely wear-resistant and often last two to five times longer than components treated with conventional heat treatments such as hardening, carburizing, nitriding, nitrocarburizing, and induction hardening.
Process Steps
The boron diffusion process is a two-step reaction:
Initial Reaction: The first step involves a reaction between the boron-yielding substance or compound and the part, dependent on time and temperature. This produces a thin, dense boride layer.
Diffusion: This is followed by a faster diffusion process.
The thickness of the boride layers varies based on:
• Temperature
• Treatment time
• Material
While the FeB layer is harder, it is more brittle and prone to fracture upon impact.