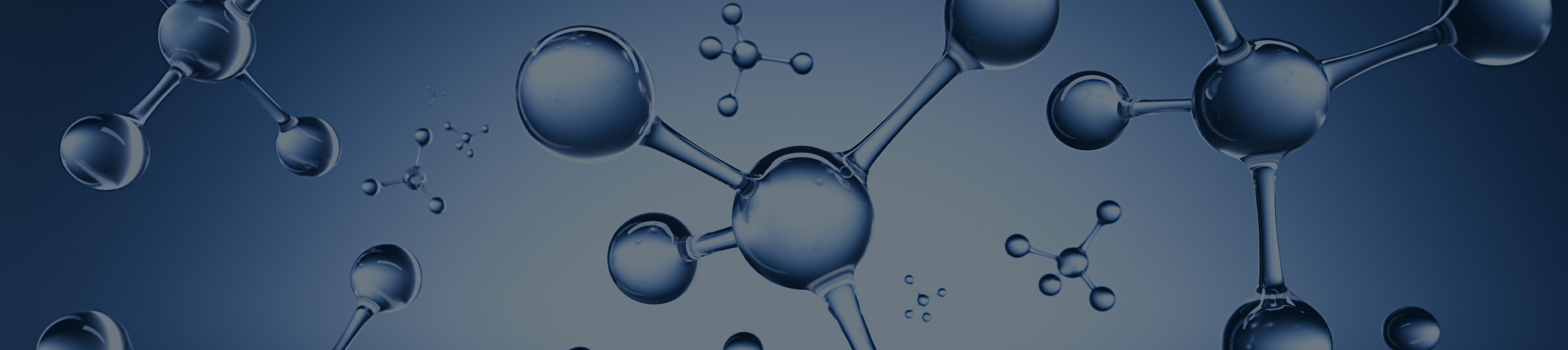
Chromising: What is it and What can be Chromised?
Chromising, also known as chromizing, is a surface treatment process used primarily to enhance the properties of metals, particularly steel.
Here are our top 10 facts about chromising:
1. Purpose: Chromising is employed to improve the surface hardness, wear resistance, and corrosion resistance of metal components, primarily steel.
2. Process: The chromising process involves diffusing chromium into the surface of the metal substrate, typically through a chemical reaction at elevated temperatures.
3. Chromium Source: Chromium, typically in the form of chromium powder or chromium-containing compounds, serves as the source material for the chromising process.
4. High Temperatures: Chromising is carried out at relatively high temperatures, often in the range of 850°C to 1050°C (1562°F to 1922°F), depending on the specific application and the material being treated.
5. Diffusion: At elevated temperatures, chromium atoms diffuse into the surface of the metal substrate, forming a chromium-rich layer.
6. Alloys: Chromising can be applied to various steel alloys, including carbon steels, stainless steels, and certain tool steels, among others.
7. Advantages: The main advantages of chromising include increased hardness, improved wear resistance, enhanced corrosion resistance, and the ability to withstand high temperatures.
8. Applications: Chromising finds applications in industries such as automotive, aerospace, oil and gas, and manufacturing, where components are subjected to high wear and corrosion environments.
9. Compatibility: Chromising is compatible with various surface finishes, including polished, ground, and shot-blasted surfaces, making it versatile for different applications.
10. Quality Control: Quality control measures, such as monitoring temperature, time, and chromium content, are critical in ensuring the effectiveness and consistency of the chromising process.
These facts highlight the significance and versatility of chromising as a surface treatment method for enhancing the performance and longevity of metal components in various industrial applications.
Here are the top 10 things that can be chromised:
1. Engine Valves: Chromising engine valves can improve their wear resistance, ensuring longevity and efficiency in combustion engines.
2. Gears and Gear Shafts: Chromising gears and gear shafts enhances their surface hardness, reducing wear and increasing their lifespan in machinery.
3. Piston Rings: Chromised piston rings exhibit improved resistance to friction and wear, crucial for maintaining engine performance and efficiency.
4. Tooling: Chromising tools such as drills, milling cutters, and dies enhances their hardness and wear resistance, prolonging their lifespan and improving machining accuracy.
5. Turbine Blades: Chromising turbine blades used in aerospace and power generation industries enhances their resistance to high temperatures and corrosion, crucial for efficient turbine performance.
6. Pump Components: Chromising pump components such as impellers and casings improves their resistance to abrasion and corrosion, extending their service life in fluid handling applications.
7. Shafts and Bearings: Chromising shafts and bearings increases their surface hardness, reducing friction and wear in rotating machinery such as engines and industrial equipment.
8. Fasteners: Chromising fasteners like bolts, nuts, and screws improves their corrosion resistance, ensuring structural integrity and longevity in harsh environments.
9. Extrusion Dies: Chromising extrusion dies used in metal forming processes enhances their resistance to wear and deformation, maintaining dimensional accuracy and surface finish in manufacturing operations.
10. Moulds and Dies: Chromising moulds and dies used in plastic injection moulding and metal casting processes improves their resistance to wear and corrosion, prolonging their lifespan and maintaining product quality.
Chromising offers a versatile and effective means of enhancing the performance and longevity of various metal components across diverse industrial applications.