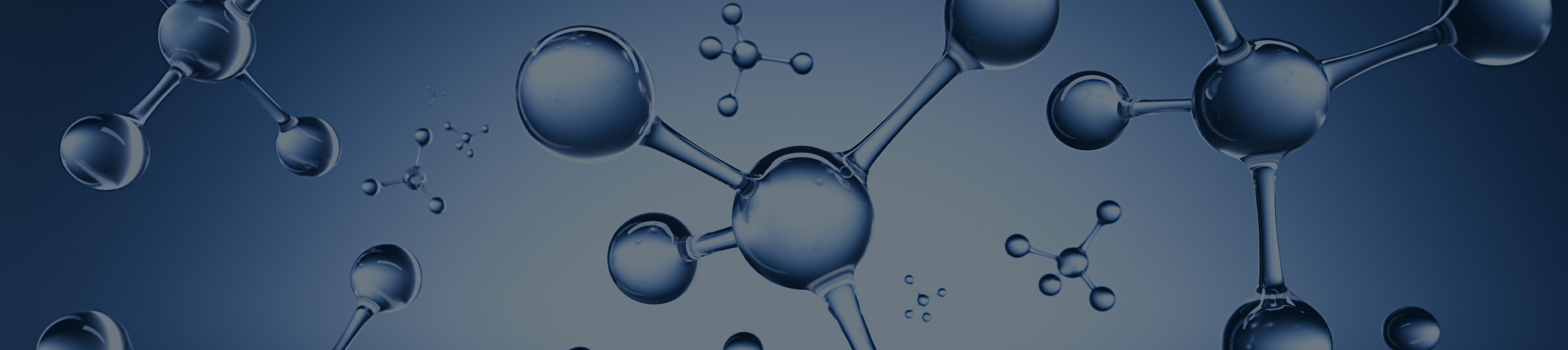
Aluminising: Understanding the Science and Application
Unravelling the Mystery of Aluminising: Exploring the Science and Application of Diffusion Coating
Aluminising, a process that involves the diffusion coating of aluminium onto a substrate material, stands as a crucial technique in the realm of surface engineering. What is the diffusion coating of Aluminising? This method not only enhances the surface properties of materials but also extends their longevity and performance in various demanding environments. Understanding the intricacies of aluminising, particularly its diffusion coating aspect, unveils a realm of scientific principles and practical applications.
At its core, aluminising involves the deposition of aluminium onto a substrate, typically through a diffusion process. This diffusion coating alters the surface composition of the substrate, imparting it with desirable properties such as enhanced corrosion resistance, oxidation resistance, and even improved electrical conductivity. The diffusion process ensures that the aluminium atoms penetrate into the substrate material, forming intermetallic compounds that bind tightly with the substrate.
The diffusion coating of aluminium typically occurs through various methods, each tailored to specific applications and material requirements. One common approach is pack aluminising, where the substrate is packed in a mixture of aluminium powder and an activator, such as ammonium chloride, and heated to promote diffusion. Another method involves the use of vapour-phase aluminising, where aluminium is vaporised and deposited onto the substrate surface in a vacuum or controlled atmosphere.
The science behind diffusion coating lies in the kinetics of solid-state diffusion. As the substrate material is heated, atomic mobility increases, allowing aluminium atoms to migrate into the substrate lattice. The diffusion rate depends on factors such as temperature, time, composition, and the presence of any surface contaminants. Understanding these parameters is essential for controlling the coating thickness, composition, and quality.
Aluminising finds extensive applications across various industries, ranging from aerospace to automotive, and even in everyday consumer products. In aerospace, aluminised components exhibit superior resistance to high temperatures and corrosive environments, making them ideal for gas turbine engines and aerospace structures. In the automotive sector, aluminised parts provide enhanced durability and resistance to exhaust gases, contributing to improved engine performance and longevity.
For further exploration of aluminising and diffusion coating techniques, a plethora of scholarly resources and research papers are available. “Diffusion in Solids” by Paul Shewmon provides a comprehensive overview of diffusion phenomena, including its applications in surface engineering. Additionally, “Surface Engineering: Science and Technology” by J.P. Celis and R.F. Speyer delves into the principles and practices of surface modification techniques, including aluminising.
In conclusion, aluminising with its diffusion coating aspect emerges as a powerful tool in surface engineering, offering a multitude of benefits across diverse industries. Through an understanding of the underlying scientific principles and practical applications, engineers and researchers can harness the potential of aluminising to enhance the performance and durability of materials in demanding environments. By continuously exploring and refining diffusion coating techniques, the future holds promising advancements in material science and engineering applications.