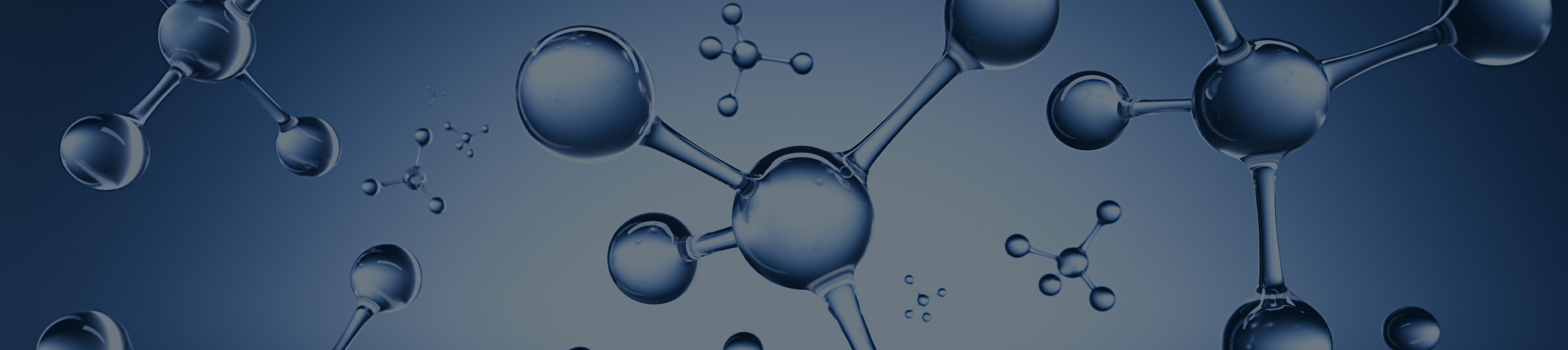
Elevate Material Performance with Advanced Diffusion Coating Techniques
Diffusion coating is a sophisticated surface treatment method that holds immense significance across diverse industries, offering a multitude of advantages such as enhanced hardness, superior wear resistance, and improved corrosion protection.
This process involves the controlled diffusion of a coating material into the surface of a substrate, thereby modifying its properties to meet specific requirements and standards. Understanding the intricacies of diffusion coating, its applications, and benefits is crucial for businesses seeking to optimize their manufacturing processes and product performance.
At the heart of diffusion coating lies the careful selection of an appropriate coating material. Metals like chromium, aluminium, titanium, and their alloys are commonly used for this purpose. The choice of coating material is determined by the desired characteristics of the final product and its compatibility with the substrate material. For instance, chromium is preferred for its exceptional corrosion resistance, while aluminium offers lightweight properties ideal for aerospace applications.
Once the coating material is chosen, it is applied to the substrate surface in the form of a thin layer. Several techniques can be employed for this purpose, including pack cementation, chemical vapor deposition (CVD), physical vapor deposition (PVD), or plasma spraying. Each method offers unique advantages in terms of coating uniformity, adhesion, and thickness control. For instance, CVD ensures precise control over coating thickness and composition, making it suitable for applications requiring high precision.
Subsequently, the coated substrate undergoes a controlled heating process, typically in a controlled atmosphere, to facilitate the diffusion of atoms from the coating material into the substrate. This diffusion process alters the microstructure of the substrate material, resulting in significant improvements in mechanical, chemical, and physical properties. For example, diffusion of carbon atoms into steel can increase its surface hardness, while diffusion of chromium can enhance its resistance to corrosion and oxidation.
One of the key advantages of diffusion coating is its ability to create a uniform and tightly adherent coating layer, even on complex geometries and hard-to-reach areas. This characteristic makes it suitable for coating a wide range of components, from small parts like bolts and screws to large structural components like turbine blades and engine components.
Diffusion coating finds extensive applications across various industries, including aerospace, automotive, energy, and manufacturing. In the aerospace sector, diffusion-coated components are utilized in aircraft engines, where they provide exceptional resistance to high temperatures, corrosion, and wear. In the automotive industry, diffusion-coated components are employed in critical engine and transmission parts to enhance durability and performance.
Despite its numerous advantages, diffusion coating also presents certain challenges, such as the need for precise control over process parameters, cost considerations, and potential environmental impacts associated with coating materials and processes. However, ongoing advancements in materials science and manufacturing technologies continue to drive innovations in diffusion coating, making it an indispensable tool for enhancing the performance and longevity of engineered components.
In conclusion, diffusion coating represents a sophisticated yet indispensable surface treatment technique that offers a wide range of benefits across diverse industries. By leveraging the principles of controlled diffusion, businesses can achieve significant improvements in material properties, leading to enhanced product performance, reliability, and durability. As industries continue to evolve, diffusion coating is poised to remain a cornerstone of modern manufacturing and engineering processes.
Contact Diffusion Alloys for more information or to get a quote and unlock the potential of advanced surface treatments for your business.