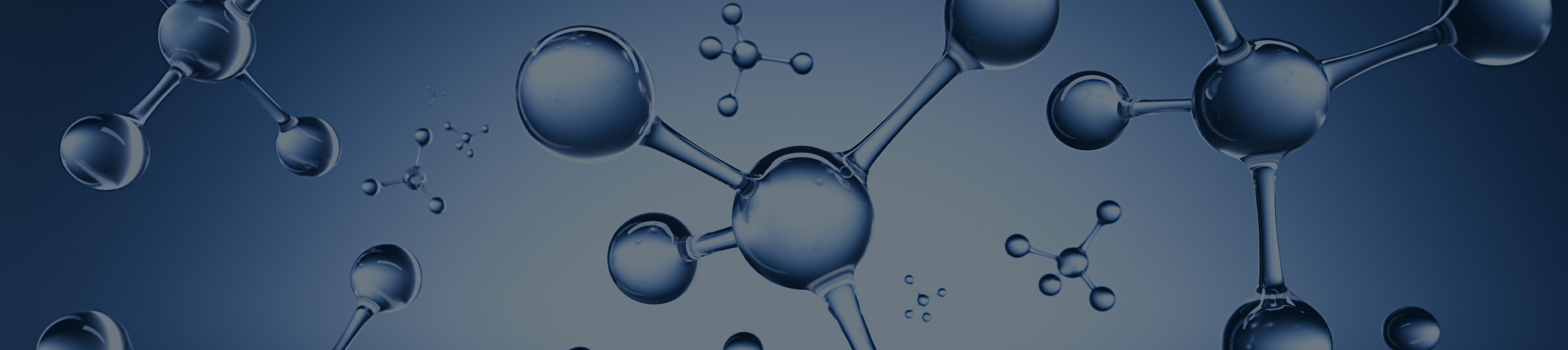
Lifetime Extension Benefits of Calorizing Copper Tuyeres in Blast Furnaces
A tuyere or tuyère is a tube, nozzle or pipe through which air is blown into a furnace or hearth.
What is a tuyere?
A tuyere or tuyère is a tube, nozzle or pipe through which air is blown into a furnace or hearth. Air or oxygen is injected into a hearth under pressure from a device such as bellows or a blowing engine. This causes the fire to be hotter in front of the blast than it would otherwise have been, enabling metals to be smelted or made hot enough to be worked in a forge. Blast furnaces are used in the smelting process for industrial metals such as iron, lead or copper. A single blast furnace is likely to have multiple tuyeres, typically made out of copper and cooled with a water jacket. Tuyeres are subjected to extreme temperatures, structural load, pig iron drops and abrasion from suspended particles.
How do they corrode?
The corrosion of copper tuyeres can cause considerable down time to a steel manufacturing operation. The corrosive attack on a tuyere consequently leads to the formation of intergranular cracks and micro porosity in the tuyere copper which can ultimately lead to a brittle tuyere which breaks when subjected to thermal stress. Tuyeres can also overheat due to the formation of high temperature iron droplets on the surface of the tuyere; ultimately causing the tuyeres to melt. Tuyeres tend therefore to be one of the most frequently replaced components in a blast furnace. The cost of replacement and the cost of the downtime can have a significant impact on the operational efficiency.
Peel Jones, in the UK, design and manufacture high conductivity copper castings and have been working in the iron and steel industry and selling tuyeres around the world for over fifty years. Some years ago, Peel Jones approached Diffusion Alloys, in the UK, to investigate the use of a protective calorized coating on their copper tuyeres to protect the surface and extend life.
How does calorizing help?
Calorizing is a chemical process whereby aluminium is diffused into the surface of the substrate material (in this case copper), forming a metallurgical aluminide surface layer. An aluminium oxide barrier is then formed at the interface of the atmosphere which provides a protective barrier between the copper substrate and the environmental conditions.
The longevity of the coating is provided by the reservoir of aluminium underneath the aluminium oxide barrier, which constantly replenishes the aluminium at the surface allowing the continuous formation of an aluminium oxide protective barrier. For this particular application, coating thickness is up to 750 microns.
Information on the efficacy of the performance of a calorized coating in a particular blast furnace environment is proprietary to the customer but on the basis of the adoption rate to date, it is evident that the additional cost of calorizing is more than justified by the extension of lifetime to the tuyeres that it provides.
About Diffusion Alloys
Diffusion Alloys is a leading specialist in diffusion coatings with over sixty years’ experience in the industry and a wide range of coating capabilities to protect against metal degradation from high temperature corrosion, metal dusting, sulfidation, wear and abrasion. For further information please contact us on:
Website: www.diffusion-alloys.com
Tel: +44 (0)1707 266111
About Peel Jones
Peel Jones designs and manufactures high conductivity copper castings to the iron and steel industry on a global basis. The company has been operating for over fifty years and provides a wide range of water cooled, high performance cast copper components for blast furnaces, steel plant, arc furnaces, smelters and cupolas. For further information please contact us on:
Email: sales@peeljonescopper.co.uk
Website: www.peeljonescopper.com
Tel: +44 (0)1287 640658